Jun 21, 2023 | Blog, Well Control, Well Integrity, Wellhead
Drilling activities involve inherent risks, emphasizing the importance of readily available equipment like the Blowout Preventer (BOP). As a critical component on every drilling rig, the BOP plays a pivotal role in controlling back pressure kicks in the wellbore, mitigating the risk of blowouts.
To ensure proper well control and prevent blowout incidents, it is vital to install BOPs with the right specifications, including size and pressure ratings. With a combination of risk assessment, compliance with legal requirements, adherence to local practices, and consideration of well type, we make informed decisions when selecting BOPs for our clients.
At Kenyon, we understand the significance of these factors and the need for regular testing, refurbishment, and thorough inspections of BOPs. Our commitment to safety extends to implementing comprehensive measures throughout our operations. Our expertise in BOP stack services enables us to provide tailored solutions that address specific drilling challenges, giving you peace of mind throughout your operations.
Contact us at info@kenyon-international.com to learn more about our comprehensive BOP services and discover how we can enhance the safety and efficiency of your drilling activities. Choose Kenyon for reliable well control solutions.
Apr 5, 2022 | Press Release, Well Integrity
The CEO of Kenyon International West Africa Company Limited, Victor Ekpenyong, at the just concluded Oloibiri Lecture Series and Energy Forum held on the 31st of March 2022, has proposed that deploying an idle well management strategy and remote well control are the two key solutions to combating oil theft which can equally maximise oil production to increase revenue and facilitate Nigeria’s energy transition.
The lecture which took place at PTDF Towers, CBD in Abuja was themed ‘Global Energy Transition: Implications on Future Investments in the Nigerian Oil and Gas Industry’ and attended by industry dignitaries.
In Victor Ekpenyong’s opening remark, he stated that oil theft has been the bane of our economy as it had led to loss of revenue and environmental pollution; and since oil accounts for the major source of revenue in Nigeria, it behooves the federal government to maximise its oil production through putting measures that deters oil theft and vandalism.
In his speech, he explained that an idle well management strategy will enable a well to be decommissioned safely to protect it from being vandalised and restore an abandoned well to full potential when necessary while remote well control is a technology that can be deployed to protect oilfields facilities and environment from hazards such as blowouts.
Victor Ekpenyong appealed to the federal government to integrate the idle well management strategy and remote well control to help reduce the number of emerging idle wells and boost oil production which can in turn help fund and facilitate a smooth transition into a clean energy.
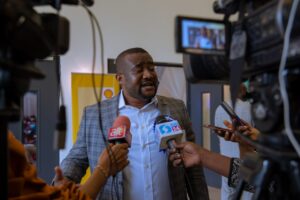
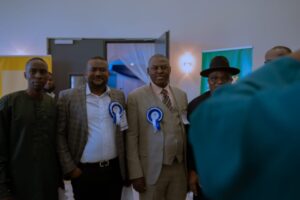
Jun 19, 2021 | Blog, Coiled Tubing, Pumping, Slickline, Well Integrity
We bid for a brownfield project on well remediation and won. We set out and planned for the job, acquiring all necessary equipment that would be needed for the job. Due to the intensity of degradation that had happened to the well, the project was categorised into three phases: well securement, well integrity and well perforations. The entire project encompassed well head team, slickline team, e-line team, pumping team, structural team, marine team, security team and catering crew.
First milestone: Well Securement
After we had conducted a thorough survey to know the amount of work that needed to be done, we mobilised a wellhead team, slickline team, etc., to the field. At the field, we liaised with the client’s production team and had the well shut in and the pressure bled off. The wellhead team ascertained the XMT integrity while the slickline team rigged up their unit and carried out drift with GC (gauge cutter) to confirm that the wellbore was free.
they ran in hole and retrieved the WRSCSSV to the surface, rigged up yet again and retrieved PXN plug, and installed a new PXN plug on the well which was pressure-tested okay. Afterwards, a new WRSCSSV was installed, and pressure tested okay. Finally, at the surface, we ran in hole and installed BPV to have a triple barrier to finish up the short string.
We proceeded to the long string which had not been producing for a long time and was shut in. BPV was installed again. We broke out the tree cap, rigged up lubricator and attempted to retrieve the existing NRV but could not. We subsequently rigged down our lubricator and ran in Lead Impression Block (LIB) to take impression of what had impeded the operation since we could not make up our NRV running tool. Using the LIB, we ascertained the internal diameter (ID) of the existing NRV and saw that it was quite smaller than the original ID of the NRV. Through our ingenuity, we designed a special tool that enabled us to retrieve the NRV from the long string. We then made up a TWCV and ran in the hole and conducted the Xmas Tree Valve checks to ensure the integrity of the valves. The NRV was retrieved and the slickline crew retrieved the WRSCSSV, retrieved the PXN and installed a new PXN plug and, afterwards, ran in a new WRSCSSV (wireline retrievable subsurface safety valve).
The three barriers were successfully established to ensure that the well was secured, and no hydrocarbon was leaking to the surface. We proceeded to the annulus valves, checked them, installed a VR plug to make sure there was no pressure or gas coming out from the annulus valve. We secured the annulus valve, nippled down the 3” XMT and installed 3” abandonment flange with a 3-1/2″ MGV + 1/2″ KTV + Pressure Gauge stop to monitor pressure. We rigged down the flowline.
Second milestone: Well integrity remediation
For the well integrity remediation, we mobilised structural team, well integrity team, piling team and casing integrity team. Once we got to the field, we signed a permit for hot work. We commenced a massive hot work on the platform to decommission the platform. Afterwards, we commenced installation of a new platform prefabricated at our base in town. We positioned the piling machine and drove in 4 platform pillars with it to the point of refusal. We filled the four pillars with cement mixtures to prevent corrosion. The structural team were able to install the new platform.
After installing it, we chipped out the cement that was between the 26’ conductor pipe and the collapsed 13’3-8 casing. We cold-cut a section of the 26” conductor pipe, beveled it to enable the installation of Gussets, hydro-blasted it and installed composite wrap on the collapsed 13’ 3/8 casing to restore the integrity of the casing. The composite wrap was left for some time to dry. Then, we installed 26” split pipe on the existing 26” conductor pipe and installed a gusset that was fabricated at our base. and welded them together.
The weight of the wellhead was transferred to the gusset situated atop the 26” casing. *This gave the new platform triple support to prevent it from bending. * A mud engineer finally mixed the G-class cement, ascertained the mud balance and dumped the cement inside the section of 26’ casing/gusset filled to the brim. After correcting the bend on the collapsed 13’ 3/8 casing, the well’s integrity was restored, and the structural and piling teams were demobilised.
3rd Milestone: Perforation
After refurbishing the XMT at Kenyon base, it was sent to the field. The abandonment flange that was installed on the well was nippled down for the refurbished XMT to be re-installed.
The wellhead team retrieved the NRV that was set on the long string, and then the slickline crew went ahead to retrieve the WRSCSSV, and eventually retrieve the PXN. The e-line team rigged up their unit and caried out a drift on the long string to ensure the wellbore was clear, and a subsequent C/O log was carried out to analyse the reservoir for crude content. Once that was done, we ran in and set a magna range plug, then dumped few feet of cement on top of the magna range plug, let it cure before we eventually made up the perforation gun and perforated the tubing.
As we observed crude on the surface, we then shut in the well and installed CCU. We went ahead to retrieve the NRV on the short string, shut in the well and installed antitheft to secure the XMT and the valves. Once this was completed, we handed the well over to our customer and demobilised from site.