Jun 17, 2022 | Blog, Wellhead
The choke valve being one of the valves that make up the Christmas tree plays a sensitive role during production. In upstream oil and gas industry, choke valves are used wherever there is a requirement for wellhead flow and pressure control. That is, it is used to regulate the flow of fluid to keep pressure under control. Operators are constantly monitoring the production system, and hardly do they ever open the choke valve fully because the level to which the valve is opened will determine the life of the well. This highlights the need for careful control of the flow of the well fluids to avoid any production well formation damage. A client contacted us when their wellhead adjustable choke became faulty and was affecting their production. We removed the old choke and successfully installed a new one. After the replacement of the choke valve, our client was able to optimize production.At Kenyon, our desire is to see our clients achieve their set goals within the speculated time and maximize production.We are Kenyon!
Apr 28, 2022 | Blog
Having a safety and health culture is paramount to our organisation.
In our industry, we promote conversations around safety and health to curb occupational accidents and disease.
Our safety culture has tremendously helped us in gaining our status as one of the most reliable indigenous companies in Africa with a great global positioning.
Today, we join in celebrating Safety and Health at Work globally through raising awareness on how to work safely and maintaining a clean bill of health.
For us at Kenyon, it is Safety every time and always.
Happy World Safety and Health Day
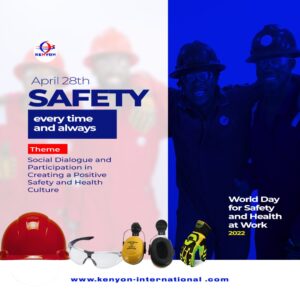
Apr 28, 2022 | Blog
The CEO of Kenyon International West Africa Company Limited, Mr Victor Ekpenyong, has, at the last Society of petroleum Engineers Young Professional Symposium held on the 23 April, 2022 in Port Harcourt, reaffirmed his resolve to continue partnering the young Professionals in ensuring that they advance and gain insights into their career paths.
He made this statement in his opening remark at the symposium held by section 103, stating that Kenyon international is devoted to empowering Young Professionals, SPE Young Professionals-YP: Port Harcourt Section, through deploying strategies that can add value to them. He equally reminded them how Kenyon International in 2020 supported Young Professional Graduates to empower their respective business ideas.
He encouraged the Young Professionals not to relent in acquiring professional and soft skills, and attend to their tasks ethically with utmost sincerity, adding that the industry gives an open access platform for those who have gained experience and acquired all the aforementioned skills to excel.
Stay tuned to find out what we have in store for Young Professionals.
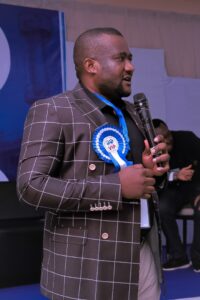
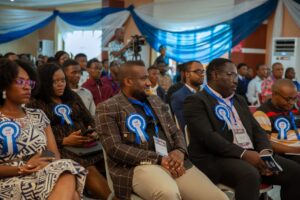
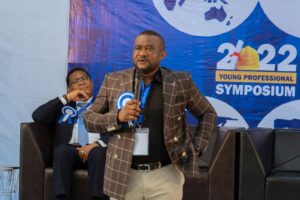
Apr 5, 2022 | Press Release, Well Integrity
The CEO of Kenyon International West Africa Company Limited, Victor Ekpenyong, at the just concluded Oloibiri Lecture Series and Energy Forum held on the 31st of March 2022, has proposed that deploying an idle well management strategy and remote well control are the two key solutions to combating oil theft which can equally maximise oil production to increase revenue and facilitate Nigeria’s energy transition.
The lecture which took place at PTDF Towers, CBD in Abuja was themed ‘Global Energy Transition: Implications on Future Investments in the Nigerian Oil and Gas Industry’ and attended by industry dignitaries.
In Victor Ekpenyong’s opening remark, he stated that oil theft has been the bane of our economy as it had led to loss of revenue and environmental pollution; and since oil accounts for the major source of revenue in Nigeria, it behooves the federal government to maximise its oil production through putting measures that deters oil theft and vandalism.
In his speech, he explained that an idle well management strategy will enable a well to be decommissioned safely to protect it from being vandalised and restore an abandoned well to full potential when necessary while remote well control is a technology that can be deployed to protect oilfields facilities and environment from hazards such as blowouts.
Victor Ekpenyong appealed to the federal government to integrate the idle well management strategy and remote well control to help reduce the number of emerging idle wells and boost oil production which can in turn help fund and facilitate a smooth transition into a clean energy.
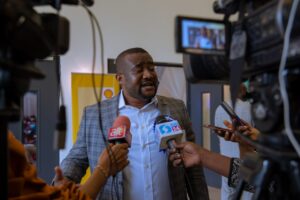
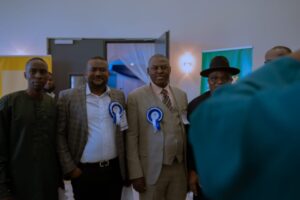
Jan 12, 2022 | Press Release, Well Control
Devastating oil spills in Bayelsa’s Nembe community from a leaking wellhead that was affecting local residents for more than a month was eventually stopped by a team of engineers from Kenyon International West Africa Company Limited, an international oil and gas servicing company owned by a Nigerian.
The OML 29 Well 1, which is operated by Nigeria’s largest indigenous oil firm, Aiteo Eastern Exploration and Production Company Limited, had been spilling unabated into the Santa Barbara River, impacting marine lives and polluting the environment until Kenyon International West Africa intervened and brought the spill to a halt.
Efforts to contain the flow from the shattered wells were futile at first. The spill was of a special type – a gas blowout, which involved 80 percent gas and 20 percent oil.
The Wellhead owner Aiteo Eastern E&P, the petroleum minister, and Nigeria’s president all promised that specialist workers would stop the spill. And contrary to widespread claims that the spill was brought under control by foreign experts, it was the expertise of Kenyon International West Africa that effectively contained the leak.
“A key feature of our response model is transparency across all stages of response to the incident” said Victor Ekpenyong, founder & CEO at Kenyon International West Africa. “ We ensured that we factored in crucial pointers such as the size and type of spill and the environmental/ economic sensitivities of the resources at risk to avoid lasting damage on the waterways as the affected aquaculture is a major source of livelihood for the people of the community” he added
According to Ekpenyong, because the organisation is highly specialised in well intervention, well remediation and idle well management, solving the Nembe spillage came naturally to them as they had done the same for other companies. “Our client base is comprised of International Oil and Gas Companies (IOCs) and Nigerian Oil and Gas Companies (NOCs).” he explained.
Kenyon International West Africa is now rapidly becoming a recognized force in providing cost-effective well control services, well intervention services, well remediation services and idle well management services. In addition, the company has successfully completed several high-level projects for customers in the African continent.
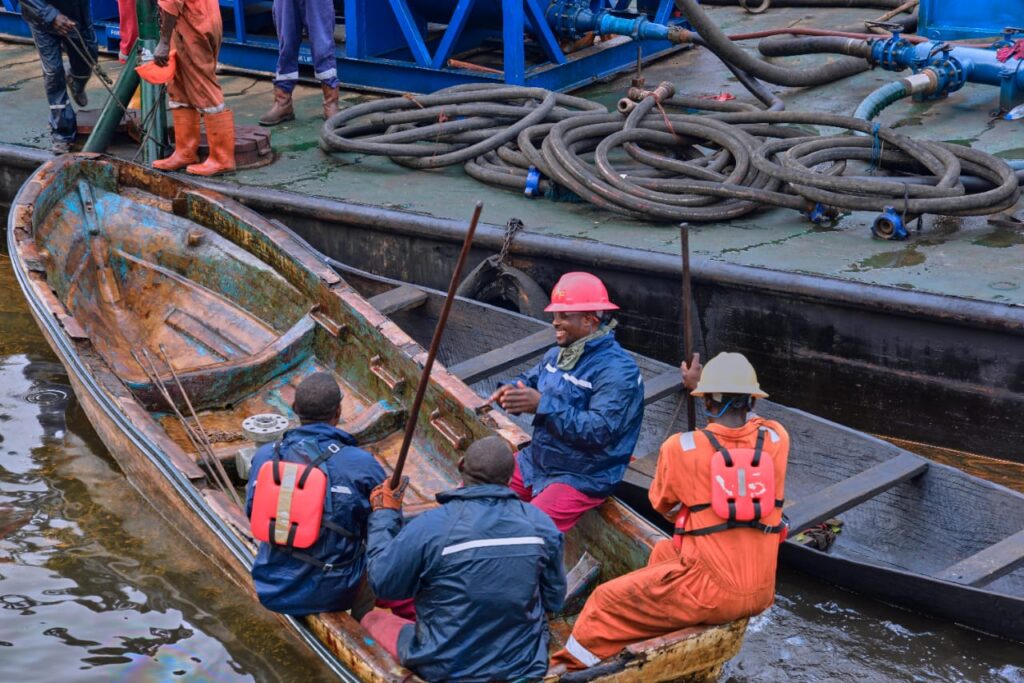
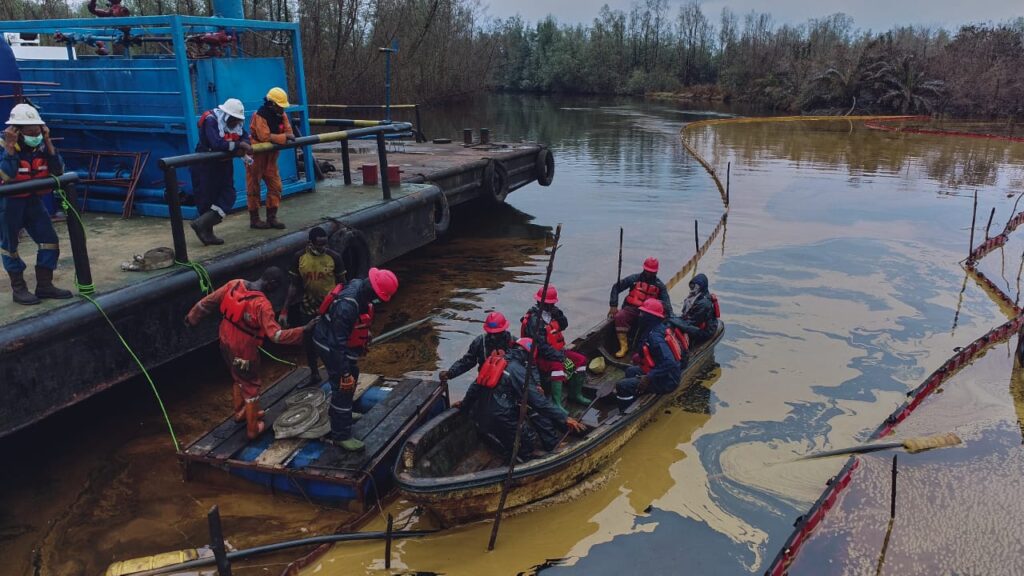
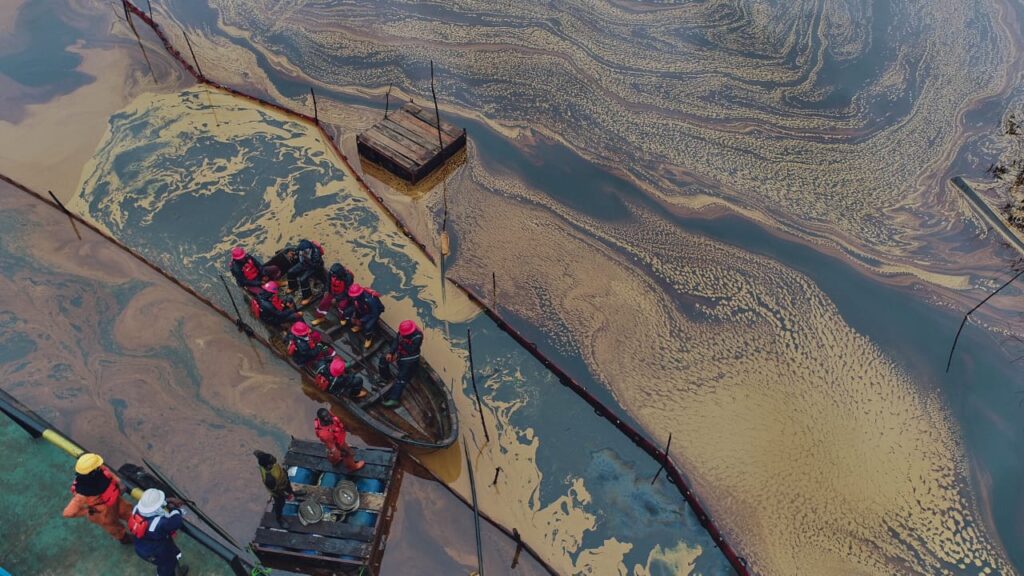
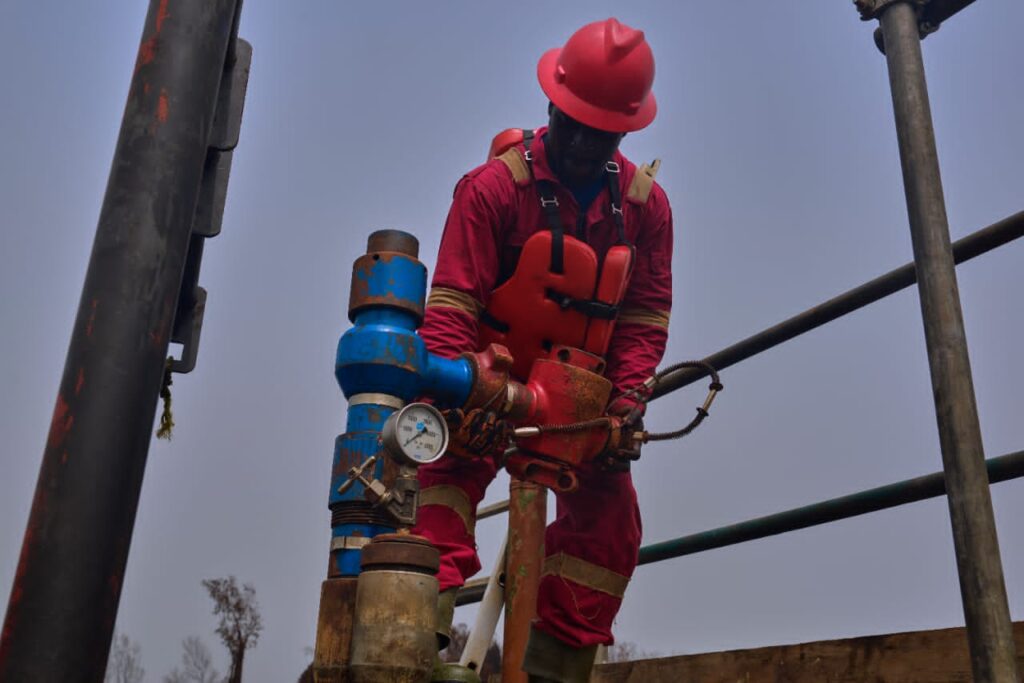
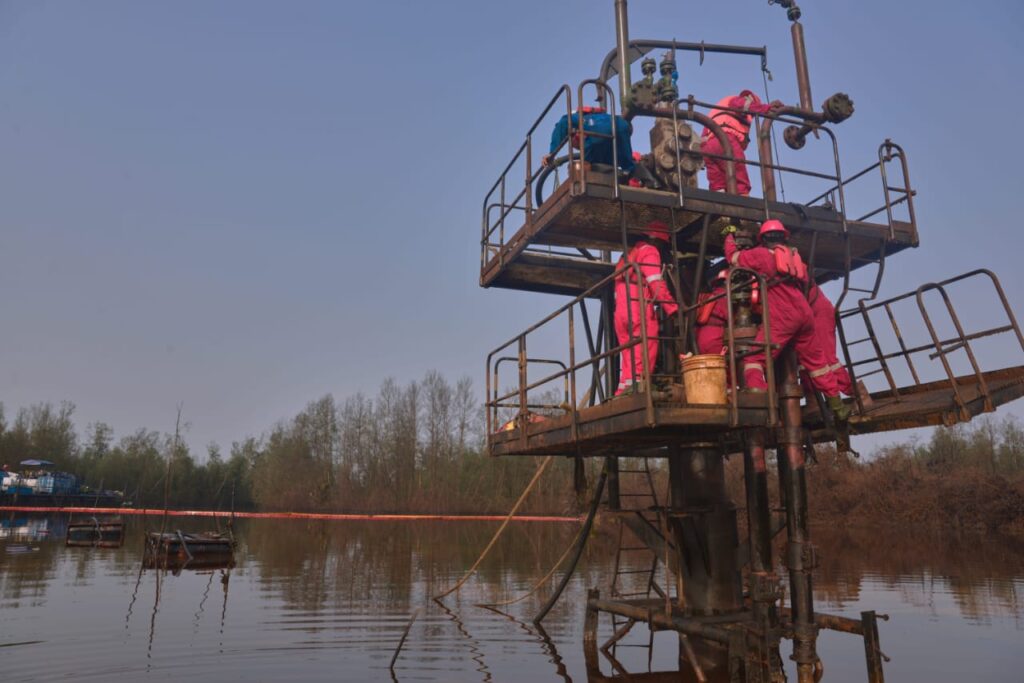
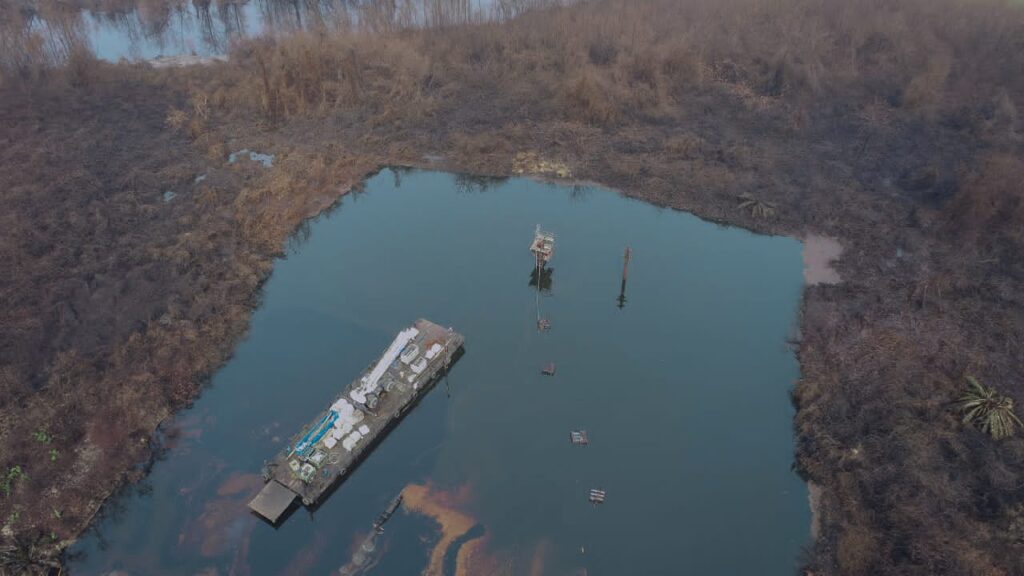
Jun 19, 2021 | Blog, Coiled Tubing, Pumping, Slickline, Well Integrity
We bid for a brownfield project on well remediation and won. We set out and planned for the job, acquiring all necessary equipment that would be needed for the job. Due to the intensity of degradation that had happened to the well, the project was categorised into three phases: well securement, well integrity and well perforations. The entire project encompassed well head team, slickline team, e-line team, pumping team, structural team, marine team, security team and catering crew.
First milestone: Well Securement
After we had conducted a thorough survey to know the amount of work that needed to be done, we mobilised a wellhead team, slickline team, etc., to the field. At the field, we liaised with the client’s production team and had the well shut in and the pressure bled off. The wellhead team ascertained the XMT integrity while the slickline team rigged up their unit and carried out drift with GC (gauge cutter) to confirm that the wellbore was free.
they ran in hole and retrieved the WRSCSSV to the surface, rigged up yet again and retrieved PXN plug, and installed a new PXN plug on the well which was pressure-tested okay. Afterwards, a new WRSCSSV was installed, and pressure tested okay. Finally, at the surface, we ran in hole and installed BPV to have a triple barrier to finish up the short string.
We proceeded to the long string which had not been producing for a long time and was shut in. BPV was installed again. We broke out the tree cap, rigged up lubricator and attempted to retrieve the existing NRV but could not. We subsequently rigged down our lubricator and ran in Lead Impression Block (LIB) to take impression of what had impeded the operation since we could not make up our NRV running tool. Using the LIB, we ascertained the internal diameter (ID) of the existing NRV and saw that it was quite smaller than the original ID of the NRV. Through our ingenuity, we designed a special tool that enabled us to retrieve the NRV from the long string. We then made up a TWCV and ran in the hole and conducted the Xmas Tree Valve checks to ensure the integrity of the valves. The NRV was retrieved and the slickline crew retrieved the WRSCSSV, retrieved the PXN and installed a new PXN plug and, afterwards, ran in a new WRSCSSV (wireline retrievable subsurface safety valve).
The three barriers were successfully established to ensure that the well was secured, and no hydrocarbon was leaking to the surface. We proceeded to the annulus valves, checked them, installed a VR plug to make sure there was no pressure or gas coming out from the annulus valve. We secured the annulus valve, nippled down the 3” XMT and installed 3” abandonment flange with a 3-1/2″ MGV + 1/2″ KTV + Pressure Gauge stop to monitor pressure. We rigged down the flowline.
Second milestone: Well integrity remediation
For the well integrity remediation, we mobilised structural team, well integrity team, piling team and casing integrity team. Once we got to the field, we signed a permit for hot work. We commenced a massive hot work on the platform to decommission the platform. Afterwards, we commenced installation of a new platform prefabricated at our base in town. We positioned the piling machine and drove in 4 platform pillars with it to the point of refusal. We filled the four pillars with cement mixtures to prevent corrosion. The structural team were able to install the new platform.
After installing it, we chipped out the cement that was between the 26’ conductor pipe and the collapsed 13’3-8 casing. We cold-cut a section of the 26” conductor pipe, beveled it to enable the installation of Gussets, hydro-blasted it and installed composite wrap on the collapsed 13’ 3/8 casing to restore the integrity of the casing. The composite wrap was left for some time to dry. Then, we installed 26” split pipe on the existing 26” conductor pipe and installed a gusset that was fabricated at our base. and welded them together.
The weight of the wellhead was transferred to the gusset situated atop the 26” casing. *This gave the new platform triple support to prevent it from bending. * A mud engineer finally mixed the G-class cement, ascertained the mud balance and dumped the cement inside the section of 26’ casing/gusset filled to the brim. After correcting the bend on the collapsed 13’ 3/8 casing, the well’s integrity was restored, and the structural and piling teams were demobilised.
3rd Milestone: Perforation
After refurbishing the XMT at Kenyon base, it was sent to the field. The abandonment flange that was installed on the well was nippled down for the refurbished XMT to be re-installed.
The wellhead team retrieved the NRV that was set on the long string, and then the slickline crew went ahead to retrieve the WRSCSSV, and eventually retrieve the PXN. The e-line team rigged up their unit and caried out a drift on the long string to ensure the wellbore was clear, and a subsequent C/O log was carried out to analyse the reservoir for crude content. Once that was done, we ran in and set a magna range plug, then dumped few feet of cement on top of the magna range plug, let it cure before we eventually made up the perforation gun and perforated the tubing.
As we observed crude on the surface, we then shut in the well and installed CCU. We went ahead to retrieve the NRV on the short string, shut in the well and installed antitheft to secure the XMT and the valves. Once this was completed, we handed the well over to our customer and demobilised from site.